The Tale of Two Clinical Supply Chains: The Risks of Fragmented Systems
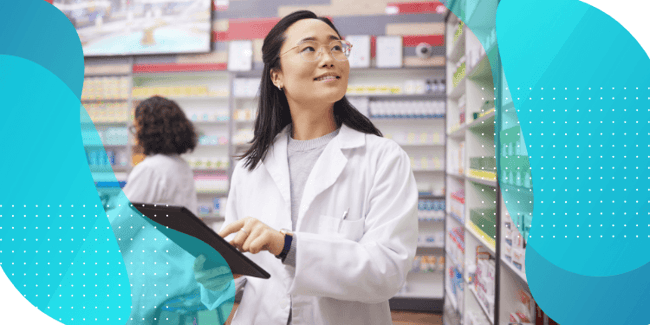
In the world of clinical trials, where every decision can make or break a pharmaceutical company's future, supply chain management plays a critical role. To illustrate two methods of managing a clinical supply chain, let’s follow Crystal, a fictitious Clinical Supplies Manager at BestPharm, as she navigates the complexities of managing pharmaceutical products in a fragmented, manual system versus a centralized inventory management system.
The fragmented approach
Crystal is tasked with managing the supply chain for a new oncology drug candidate, CP-4582. Her supply chain spans across the globe, from raw materials in China to finished patient kits in the U.S. But without a centralized inventory management system, Crystal relies on spreadsheets, emails, external inventory systems, and even paper batch records to keep track of everything. Each partner in the chain uses their own tools and processes, meaning data is scattered across multiple platforms, each with different update schedules and levels of detail.
When a genotoxic impurity is discovered in the drug substance, the stakes become even higher. Crystal needs to trace the contamination and recall affected batches, but the fragmented system forces her to contact each supply chain partner individually. She waits hours, sometimes days, for batch records to be collated, scanned, and sent back to her. As she painstakingly pieces together the supply chain information, the clock is ticking, and the risk to patient safety grows with every passing minute. The entire process could take up to 72 hours, jeopardizing BestPharm’s license to operate and their commitment to patient safety.
The centralized solution
Now, imagine Crystal’s scenario with a centralized inventory management system like Signant Health’s GxP Inventory. In this version of the story, all supply chain data is stored in one place, easily accessible and up to date. When the contamination is discovered, Crystal doesn’t have to scramble to reach out to different partners across time zones. Instead, she logs into the GxP Inventory system and generates a full lot genealogy report with the touch of a button.
The system instantly identifies the affected patient kits and batch numbers, allowing Crystal to direct her partners and clinical sites to quarantine the contaminated material. What once took days now takes less than five minutes. The risk to patient safety is minimized, and BestPharm’s commitment to quality and safety is proven, not just to the FDA, but to everyone involved in the trial.
The value of centralization
The difference between these two scenarios is clear. Without a centralized inventory management system, the risks, inefficiencies, and uncertainties of a fragmented approach can lead to delays, increased costs, and even endanger patient safety. On the other hand, a centralized system like GxP Inventory saves time, reduces risks, and protects the significant research and development investments tied to clinical investigational products.
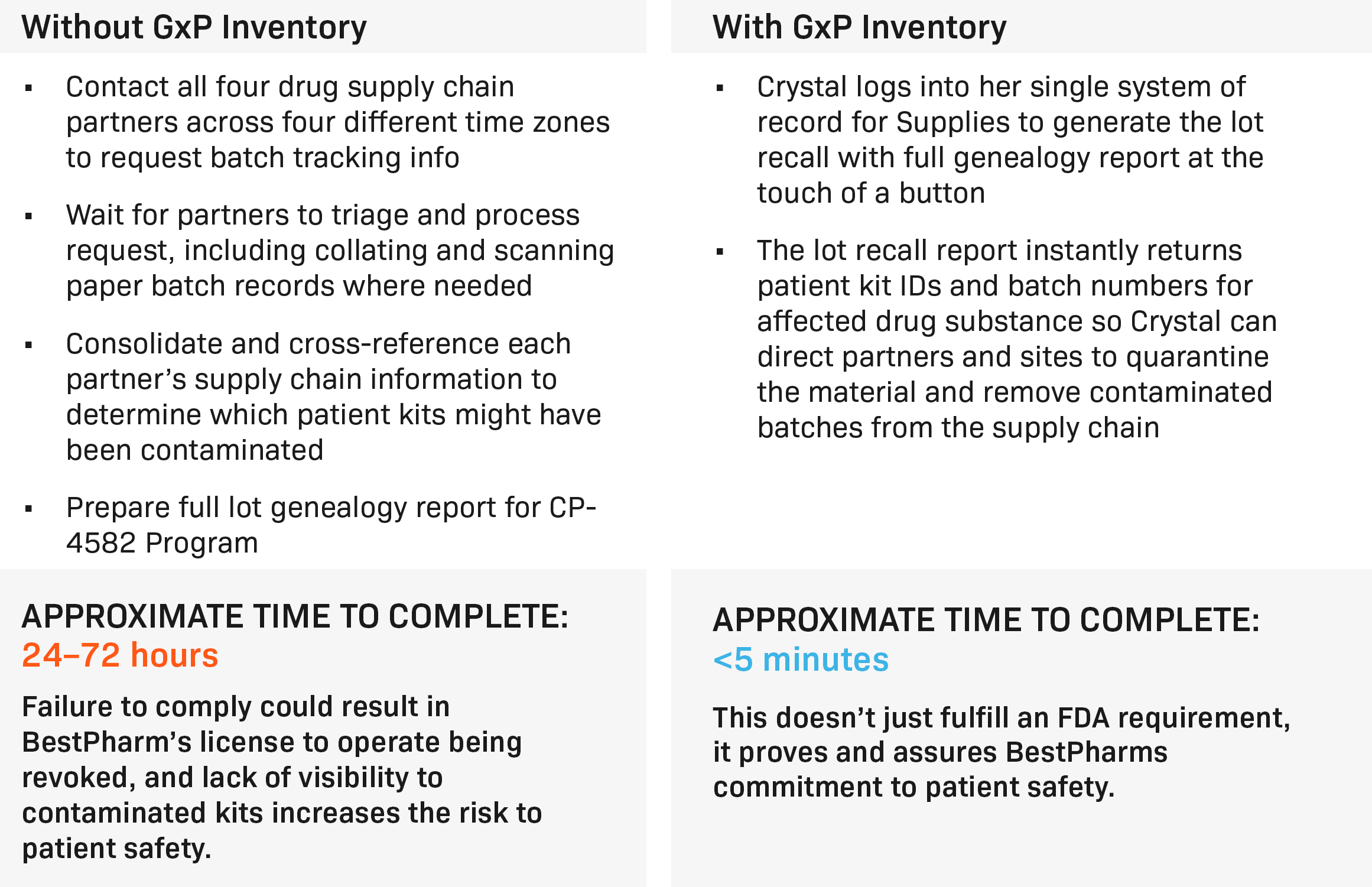
By centralizing and streamlining supply chain management, pharmaceutical companies can ensure better visibility, traceability, control, and efficiency, ultimately safeguarding their trials and their reputations. In the high-stakes world of clinical trials, where every minute counts, having a centralized solution isn't just a benefit—it's a necessity.