Single Source of Truth for Fragmented Inventory
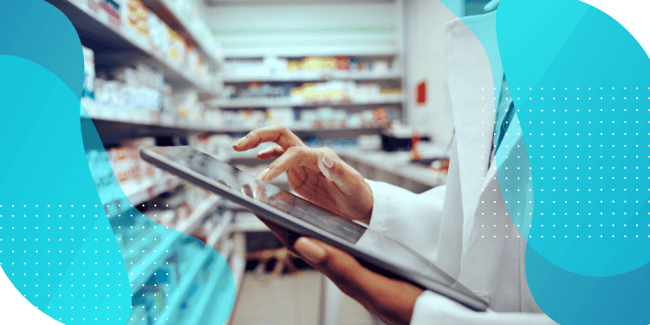
One of the most common pain points our customers face is gaining full visibility and control of their fragmented inventories. As pharmaceutical and biotech companies grow, so does the complexity of their supply chain, which is often managed by third-party vendors. This can include complex manufacturing, packaging, and labeling partners, making it increasingly difficult to maintain clear oversight of their clinical supplies.
Increasingly complex clinical supply chain
A significant challenge in clinical supply chain management is maintaining clear visibility across global operations, especially when working with multiple third-party vendors (CMOs/CROs).
Our customers operate in a highly regulated industry and gaining visibility within a single source at a global level is not an easy task and tends to require access to various systems for full supply chain traceability. This can delay decision-making, especially when quick adjustments to clinical supply levels are needed to meet evolving demands.
The challenges of fragmented inventory
- Visibility across a global supply chain
- Cumbersome, time-consuming lot recalls
- Inconsistent data accuracy
This fragmentation not only makes it harder to manage inventory levels but also complicates QA releases and regulatory compliance. Achieving the goal of delivering the right drug to the right site and patient at the right time becomes increasingly difficult without a single source of truth.
Quick and efficient lot recalls
In the event of a product compromise, sponsors must notify the FDA and produce traceability reports within 24 hours. A fragmented inventory system makes this difficult, as customers are forced to gather data from multiple systems—often leading to delays, inaccuracies, and costly errors.
Historically, managing lot recalls involved leveraging multiple external systems, pulling together numerous reports and spreadsheets, and navigating disjointed processes. This approach resulted in delays, data discrepancies, and increased costs.
See our recent blog which illustrates the lot recall experience using the fragmented data sources approach versus a centralized inventory management approach.
Signant Health’s solution to fragmented inventory
Our GxP Inventory solution solves the problem of fragmented supply chains by providing a single source of truth. This holistic system integrates all aspects of clinical supply management, from tracking inventory levels to automating workflows. With full visibility into the supply chain, customers can respond to lot recalls at the click of a button.
Key benefits of GxP inventory include:
- Complete end-to-end supply chain management: Track inventory levels, QA releases, and lot genealogy in one system.
- Cross-functional collaboration: Enable study managers, logistics, and quality teams to work within a unified platform.
- Efficient lot recalls: Rapidly respond to product recalls with accurate, real-time data.
To learn more about how GxP Inventory can streamline your clinical supply chain and increase efficiency, contact us.